
3-axis Nanopositioning Microscope Stage with Integrated Thermostat
Overview
While working as an undergraduate researcher for the Thompson Lab for Metrology of Nanosystems I was tasked with designing, manufacturing, and testing a 3-axis nanopositioning microscope heating stage to operate in a vacuum chamber. The microscope heating stage was needed for the lab to continue to develop new experimental techniques to measure heat dissipation along with material properties in nanomaterials over ultra-fast time scales such as picowatt heat flow resolution and nanosecond time response. The stage provided a stable temperature mounting location for nanofabricated calorimeters and allowed for 16 wire bonded connections to mounted chips. A Peltier module was used to heat and cool the system to +/- 1 millikelvin via PID feedback control. A PID controlled 3-axis piezoelectric movement stage in series with a manual movement stage using micrometers provided the positioning of the chip under the microscope. A centrally located thermistor recorded the temperature. Matlab was used to provide inputs to the Texas Instruments DAQ which controlled the Peltier module.
Two large copper heatsinks were designed to function with the Peltier module. The larger bottom heat sink (“Hot” side) was sized to be at least 2x the volume of the top heat sink (“Cold” side) to adequately dissipate the heat from the sample carrier. Copper 110 was used due to its machinability and its oxygen free, high-purity nature making it excellent for operation under vacuum conditions. I machined the heatsinks and the piezoelectric mounting plate (6061 Al) at our machine shop using a 3-axix CNC mill.
Processes Utilized
3D Modeling & Rendering (Solidworks)
PID Control Tuning
CNC Machining
Wiring
Top Skills Utilized
CAD modeling
Mechanical Design
Design for Vacuum
CNC Machining
Matlab
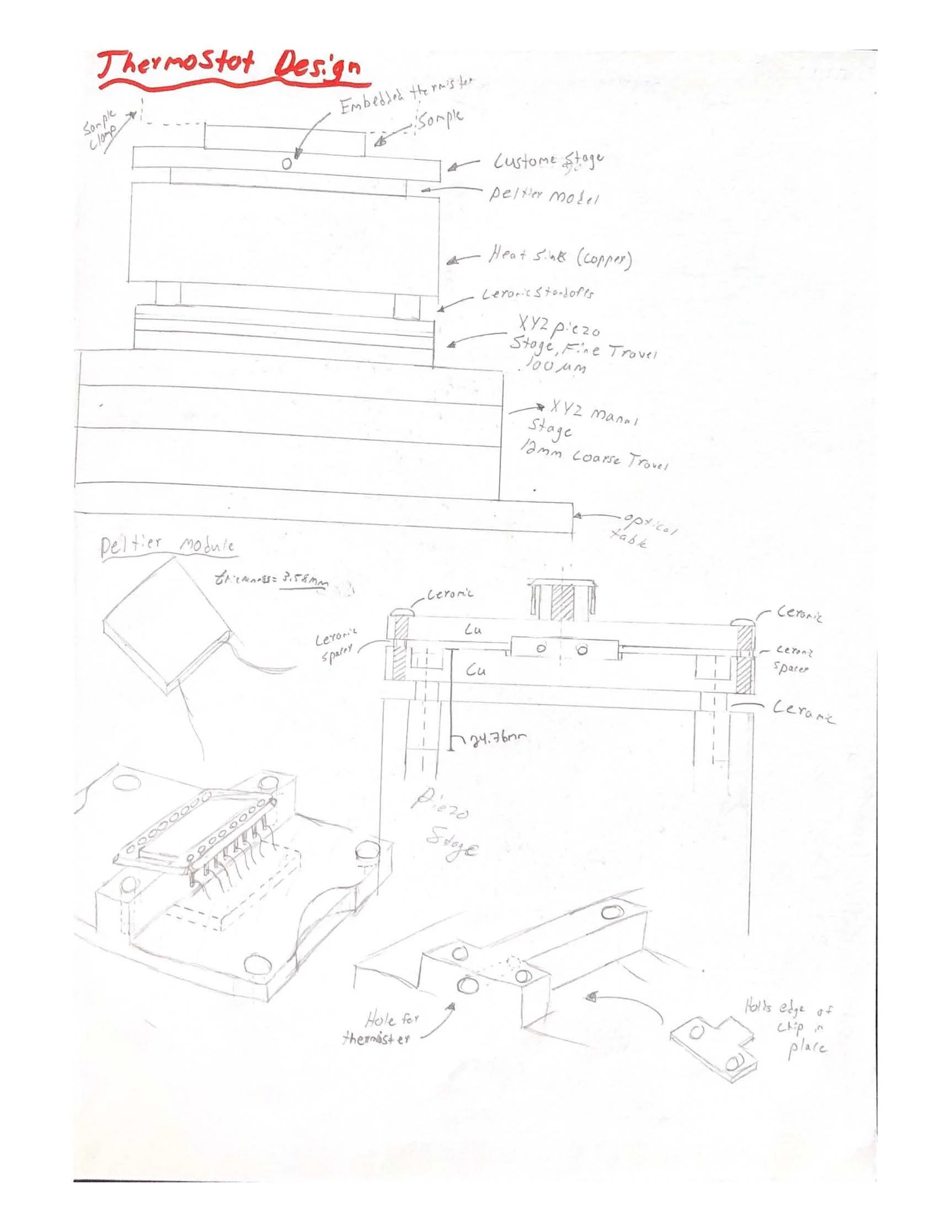
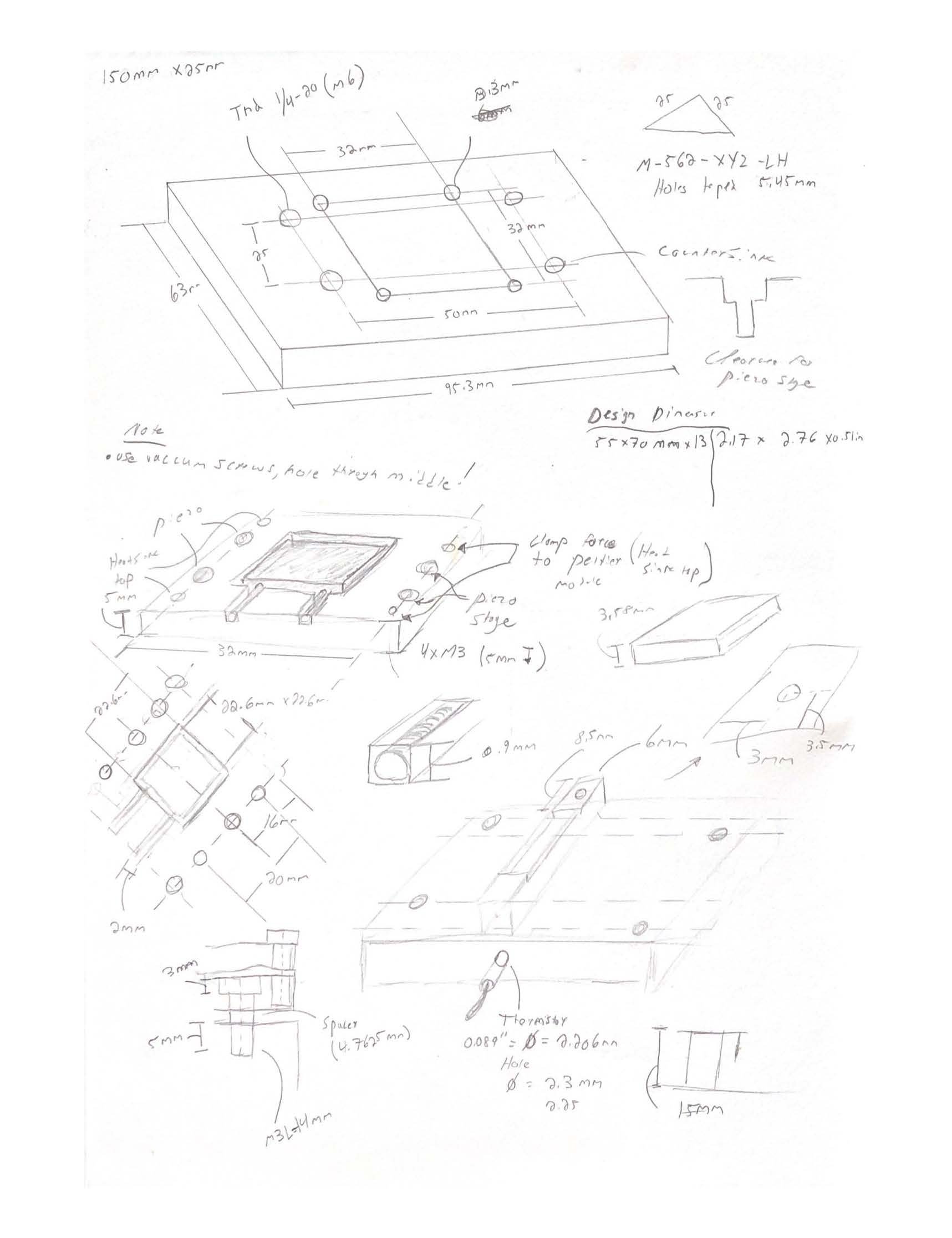
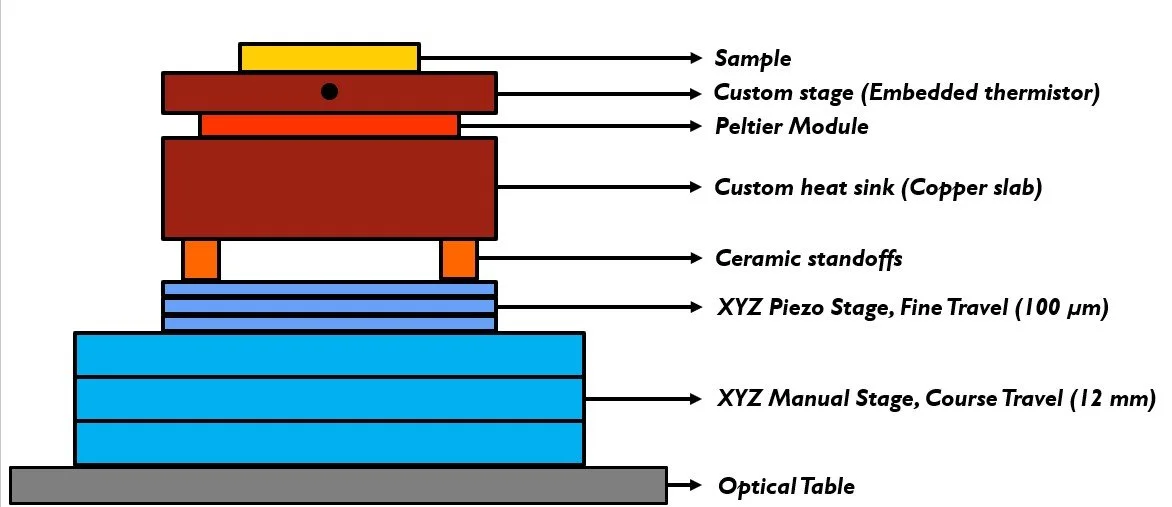
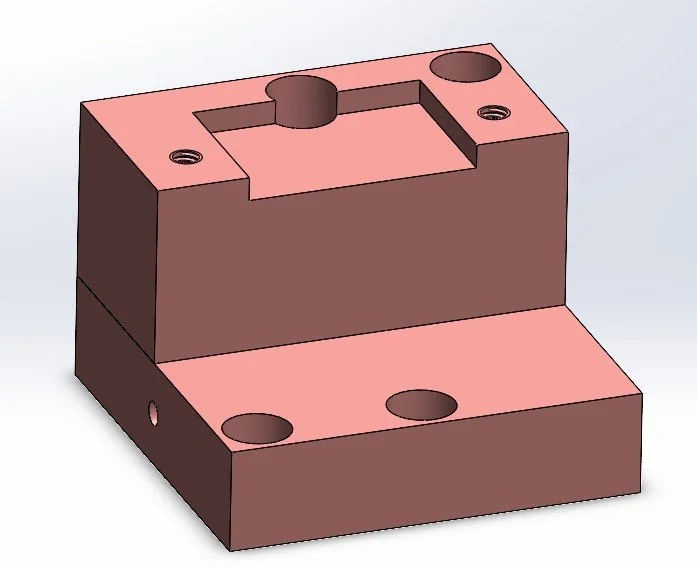
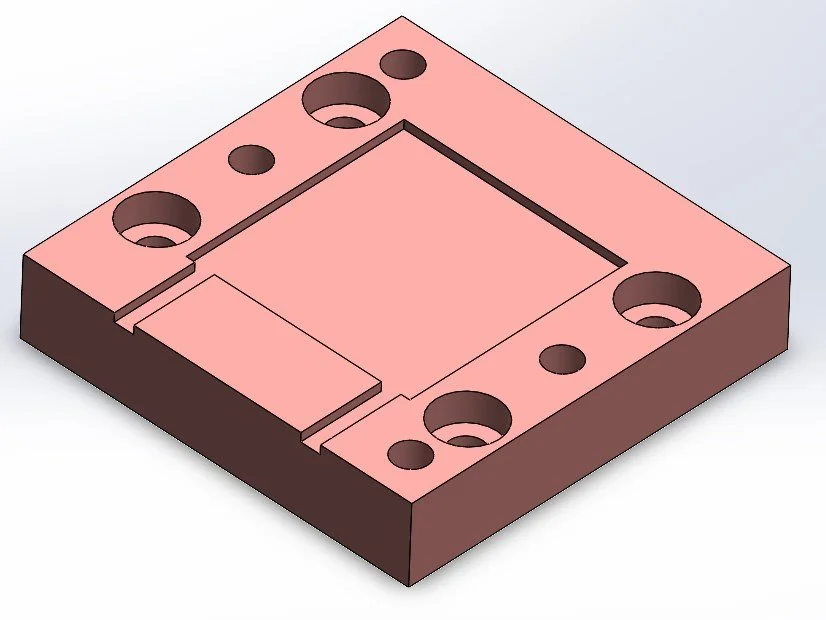
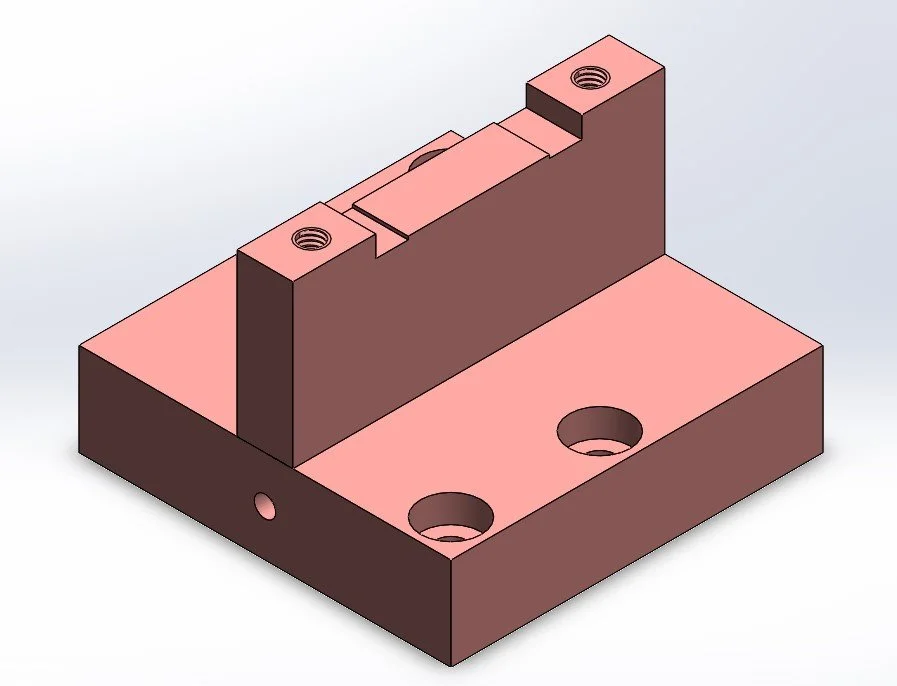
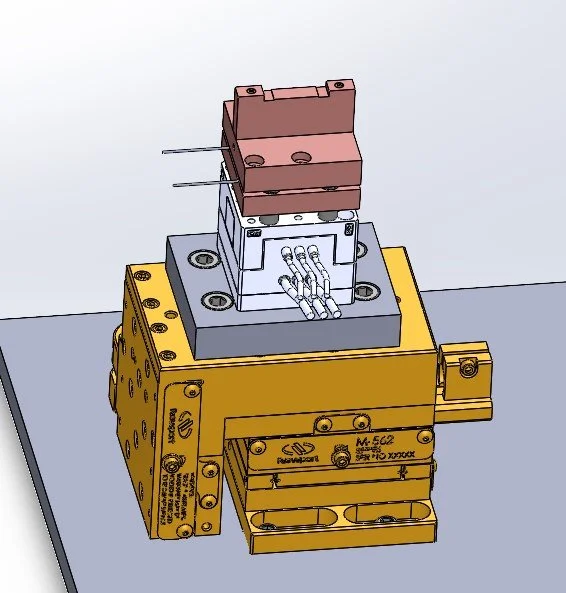

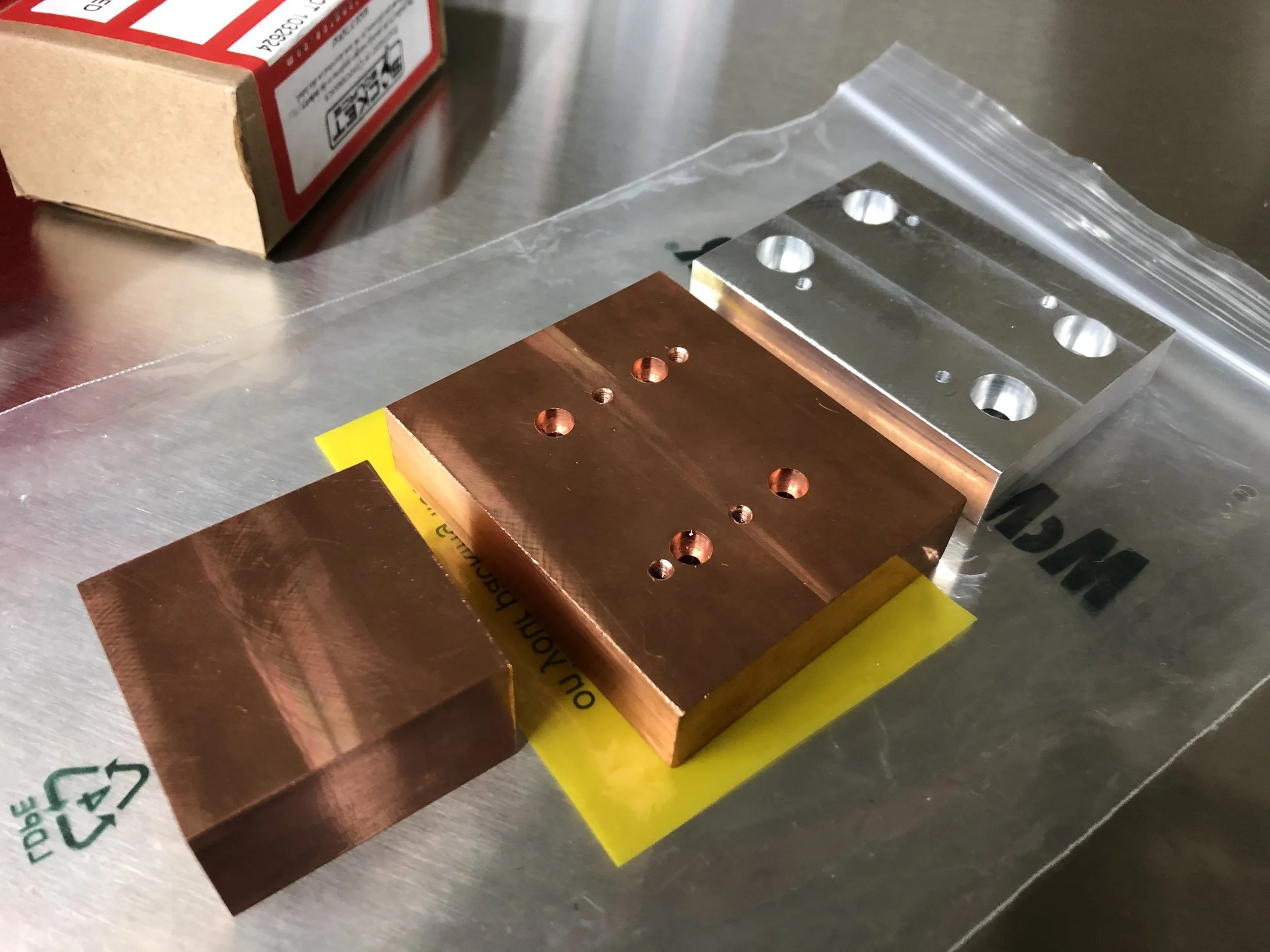

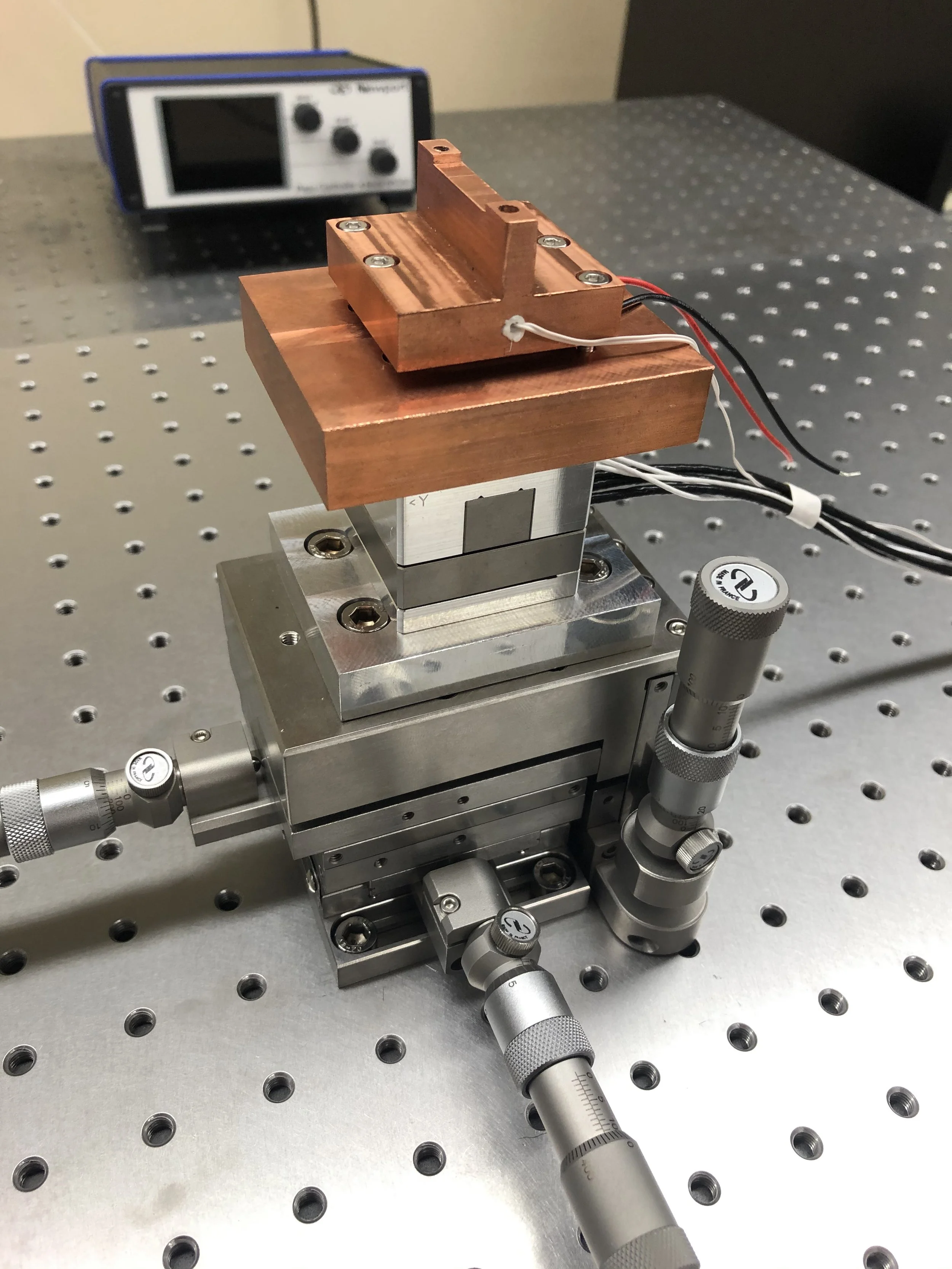
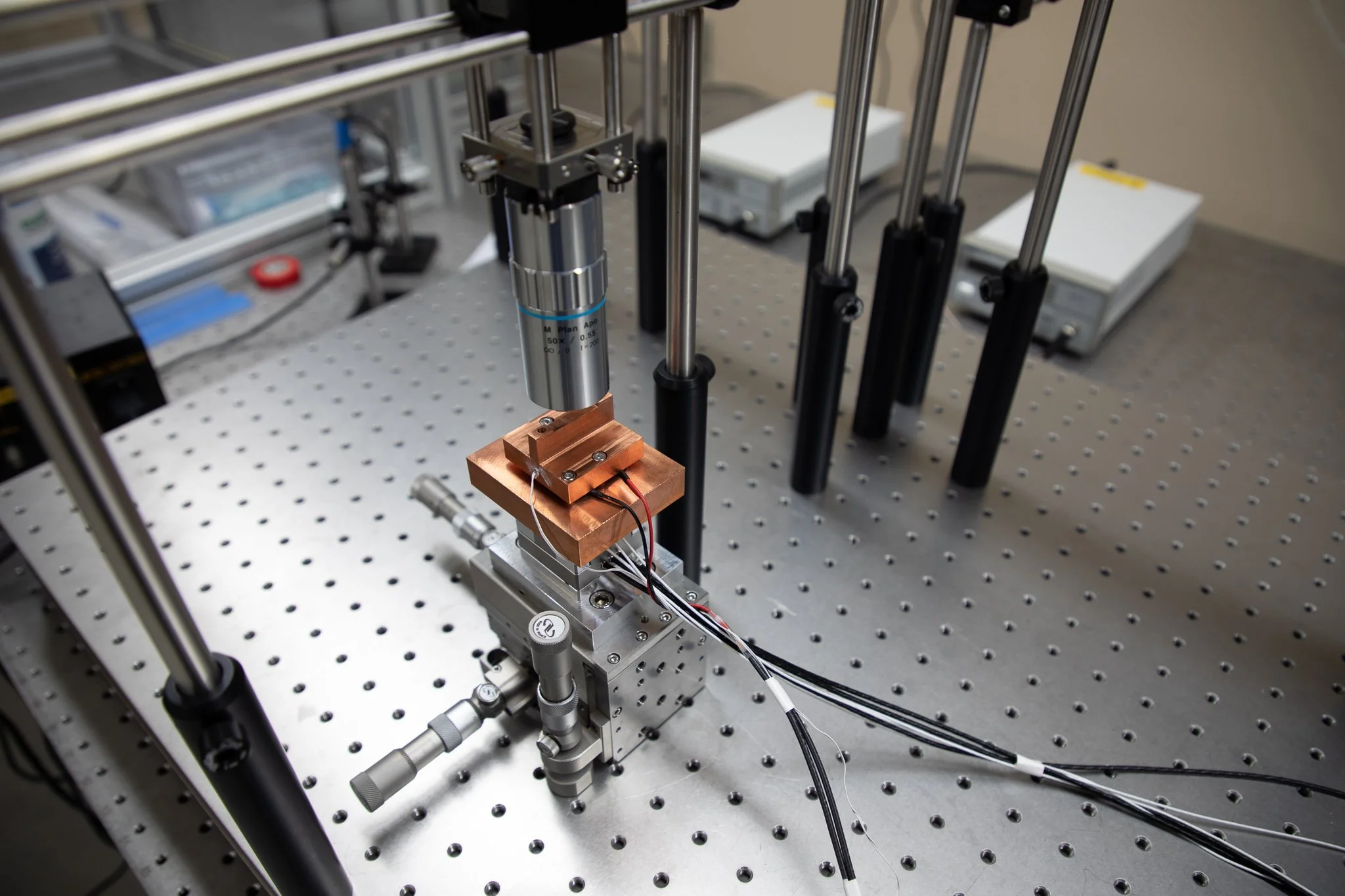